新工場建設プロジェクトは、一人ひとりの挑戦と成長の場
沢井製薬の生産・製造職は、決められた作業を黙々とこなすだけの仕事ではありません。
製造する製品が頻繁に変わる中で、日々勉強を重ね、部門を超えて協力し合う。後輩社員教育なども若いうちから任されます。また、経験を活かしつつ、成長するためのチャンスも与えられます。ジェネリック医薬品業界のリーディングカンパニーとして、昨今の医薬品不足解消を目指し始まった第二九州工場新棟建設プロジェクトは、生産・製造職一人ひとりの挑戦と成長の場でもありました。
メンバー
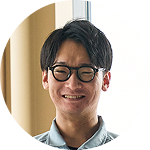
S.Y
製造2部製剤1課所属
高等専門学校電子機械工学科卒業
2014年 新卒入社
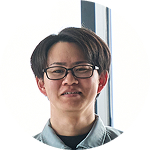
T.N
製造2部製剤1課所属
高等学校総合学科健康スポーツコース卒業
2015年 新卒入社
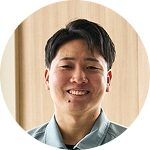
S.H
製造2部包装1課所属
工業高等学校電気科卒業
2017年 新卒入社
プロジェクト計画・概要
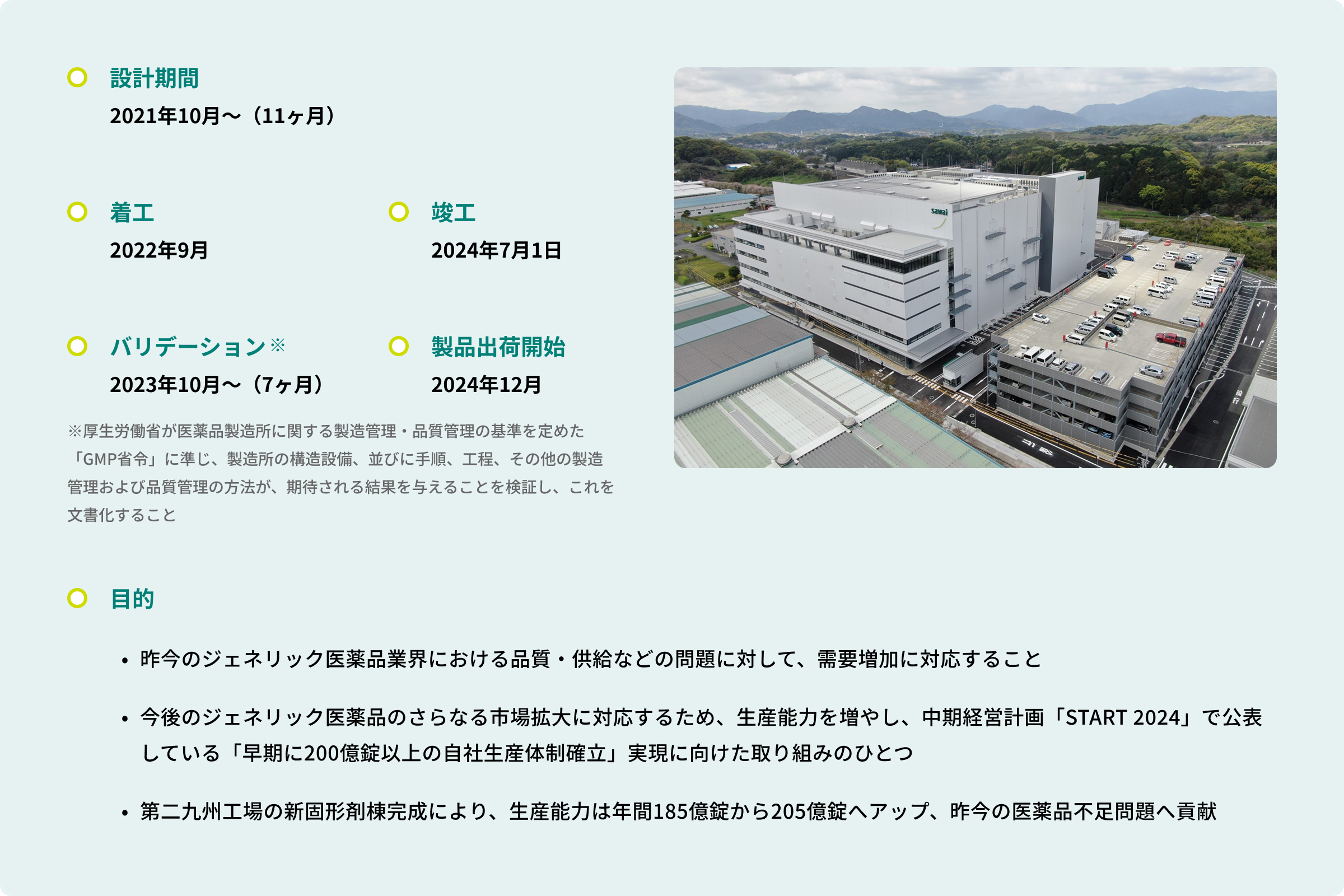
プロジェクト参画前は成長の日々。メンバーの教育にも携わる
プロジェクト参画前はどんな業務を手がけていましたか?
私は兵庫県にある三田工場で、工場設備の日々の点検、予防保全、中長期保全計画の立案などに携わっていました。特別高圧、高圧電気設備の保安業務も私の担当。業務には国が定めた電気主任技術者という資格が必要で、入社3年目のときに3種を取得しました。
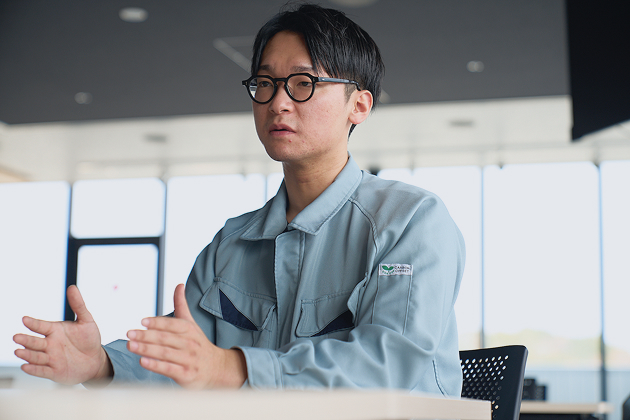
入社後すぐに建設が始まった三田西工場のプロジェクトの立ち上げにも、設備管理者として参加しています。電子機械工学科出身で建築に関しては知見がありませんでしたので、図面の読み方も建設用語も分からず勉強するしかない。もう勉強ばっかりしていましたね(笑)。建築知識を身に付けながら、三田工場の大規模改修工事も主担当として2件ほど経験しています。
入社2、3年目ぐらいからは、契約社員や工場で作業を行う工場正社員の作業を確認、指導する役割も担っていました。
私は健康スポーツコースを卒業後、新卒で入社。第二九州工場の旧棟で、打錠機といわれる装置に原材料を混合した粉末を投入し、固めて錠剤に成形するオペレーション業務を担当していました。設計部門が決めた形状、硬さ、重さになるよう打錠機の入力数値などを調整していく仕事です。
一つの種類の薬をずっとつくり続けるのではなく、切り替えながら多くの品目を製造していきます。短いと2日に一度、製造する品目を切り替えます。その都度、部品を分解、洗浄していきます。
入社4年目からは、新入社員の教育などを担当するようになりました。また、工場は交替勤務で、メンバーを早番、遅番と入れ替えているのですが、チームの人員配置や、残業が必要だったら誰を割り当てるかを考えるような業務も担当していました。
私は第二九州工場の旧棟で、錠剤などを包装するPTP充填機のオペレーションを担当していました。
PTP充填機とは、ポリ塩化ビニル(プラスチック)でつくられたポケットに錠剤などが充填され、それをアルミ箔でシールした後、シート状の型に打ち抜く包装の機械です。打錠工程で錠剤がつくられて、さらに飲みやすくする等のためのコーティング剤をまとわせる工程や文字を印字する工程などを経て、私の工程でパッケージするイメージです。
その他には、新しい機械が導入されれば最初に任されて使い方を覚え、それをチームメンバーに共有する役割も担っていました。
新棟建設プロジェクトにオファーされたときの気持ちは?
「やったー」という気持ちと「大変そうだな」と思う気持ちが半々でしたね。やはり、声がかかったのは日々の業務を評価してくれたからだと思います。それは素直に嬉しかったですね。
一方で私が任されたのはMES(製造実行システム)というシステムの構築です。原材料の入荷から完成した製品の出荷までを管理するMESの中で、打錠工程で使われる指図といわれる文書を電子化することでした。打錠機オペレーションの経験を活かしてのことでしたが、パソコンはプライベートでもほとんど触れたことがなかったため大変でしたね。
私はあるとき、上長に新機種導入後の業務に関わったと話をする機会があり、そこから1週間後ぐらいに「新工場で新しい機械の導入を任せたい」と言われました。
不安とワクワク、どちらもあったのですが、不安の方が大きかったですね。機械が現場に据え付けられて最初に触れることはありましたが、新しい機械を一から導入した経験はありませんでしたので。
私は工場立ち上げや改修工事を経験していましたので、その経験を活かして、設備管理課のマネージャーがチームリーダーとなる分科会の実質的な2番手として、プロジェクトに参加することになりました。
もともと第二九州工場とは別の三田工場で勤務していましたし、当時福岡に来たこともなかった。でも、不安はなかったですね。何とでもなるし、何とでもするぞ、といつも自分に言い聞かせていましたので。
壁を乗り越える原動力は、コミュニケーションとチームのつながり
プロジェクトで大変だったことは?
これまで指図(各製造工程での具体的な手順書)を見ながら製造をしていましたので、紙だったものがデジタルに置き換わるぐらいは理解していたのですが、作業は予想以上に複雑でした。
製造工程でどう作業が分岐していくかパターンを洗い出して、条件式を組み立て、全体を組み上げていきます。数字等の記録や集計も、これまではオペレーターが電卓で計算していたのですが、すべてシステム上で計算するようになりました。その条件設定や計算式の構築に苦労したことを覚えています。
ミスがないように心掛けたつもりですが、作成した電子指図を使った検証のための試運転では、はじめの1ヶ月間ぐらいは、エラーが頻発してしまいました。
大変だったことの一つは、工場に電気を引き込む業務です。
新棟の受電電圧は6万6000ボルト。以前経験していたものが2万2000ボルトで、ここまで大規模のものは経験がありませんでした。工場の前の道路を工事して変電所から専用ルートをつくらなければならないという、まるで変電所を一つ建設するような作業でした。電気主任技術者資格も、私が持っている3種の上の2種が必要でしたので、また勉強するのかと(笑)。工事を進めながら資格も取らなければならず、プロジェクト開始から1年ぐらいは大変でした。
さらに電気を引いたら終わりではありません。その後は、部屋のレイアウトや工場で使われる設備の配置などを取りまとめ、建設会社に伝えていく業務を担当しました。プロジェクトの各チームや各製造工程の担当部門によって、どの設備をどこに設置したいかや、コンセントの位置や数などが違います。それぞれの意見を集約するのは非常に苦労しました。
包装工程の作業エリアのレイアウトの検討や機械設備の仕様を検討することが私のプロジェクトチームの役割でした。包装機械は通常、生産する品目によって交換パーツを組み合わせて生産します。標準のパターンはありますが、カスタマイズが可能です。生産する品目によってどのパーツを使えばいいか、その選定が難しかったですね。
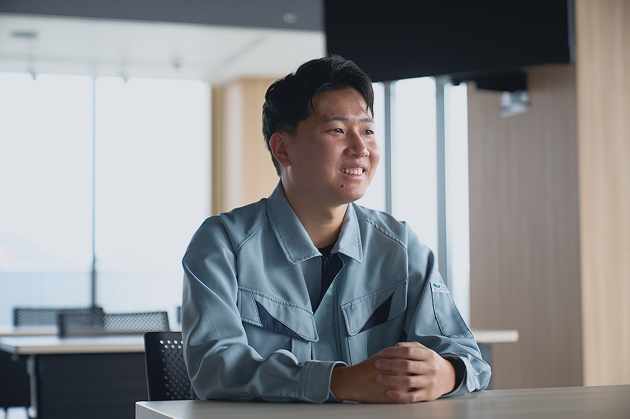
どのように壁を乗り越えていきましたか?
プロジェクト開始当初は、経験が不足していましたので、本社の関係部署や機械メーカーとコミュニケーションを取りつつ、周りの方や先輩にアドバイスをいただきながら乗り越えていった感じです。
パーツ選定の際は、包装資材のサイズや仕様を管理している部署とやり取りを重ねました。資材を購入するときは、資材のデザインやパッケージの設計を管理している部署と連絡を取りつつ、工期に間に合わせるよう資材を手配していきました。
私もコミュニケーションが一番重要でした。例えば、「部屋にコンセントが4ヶ所ほしい」と言われたとき、できればほしいのか、絶対にほしいのか、直接コミュニケーションを取りながらでないと分からないこともあります。そういうやりとりはメールなどでは難しかったので、担当者と直接会話する場面がたくさんありました。
私もそうですね。システムエラーのほとんどはパソコンの画面上で状況を確認できるのですが、直接現場に出向いて、担当者から状況を聞かなければならないものもありました。
その中でも特に密なコミュニケーションが必要だったのは、設備メーカーのシステム担当者です。何度も電話でやり取りをしながらエラーの状況を説明し、解決策を一緒に練っていきました。
常に会話をしながら進めていったイメージですね。
例えば、設備機器の選定や購入の際でも、実際に現場で使用するメンバーに不満な点や改善すべき点などをヒアリングをしてもらい、それを参考にして仕様を詰めていきました。
私が所属していたシステムチームのメンバーも、現場で包装業務を実際に行っていた方に、包装工程の電子指図を確認してもらいながら1つずつ進めていきました。
また、生産で使う備品の種類や名称などは、生産チームに逐一確認、連携しながら電子指図をつくっていきました。
日々の業務での連携だけではなく、困ったときは助け合います。工場にはいろいろな専門分野を持ったメンバーがいて、そういう人たちが協力し合うためにチームがあるのです。
私自身、インフラ関係の理化学試験で思ったような結果が出なかったことがあり、電気系が専門の私には何が原因かが分かりませんでした。そういうときに、理化学系の品質管理のチームメンバーが、自分の業務外のところでも、原因の特定や解決方法を探すために進んで協力をしてくれました。チームのつながりは大事だと改めて気づかされたため印象に残っています。
生産・製造職として、一つ上の視野を持つことができた
プロジェクトを通じて、一番印象に残っていることは?
電子指図は、製造作業の初心者を含めて誰が見ても「同じ作業で同じ品質のものをつくることができるように」というコンセプトでつくられました。
実際に今まで紙の指図で作業をしていたオペレーターから、「電子化されてすごく分かりやすくなり、ミスもしにくい」と直接声をかけられたときは、本当によかったと思いました。電子指図導入の目的であり、自分が担当した部分で成果が出たので達成感がありました。
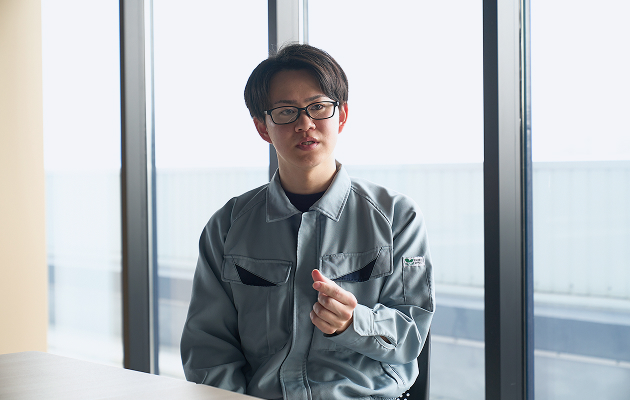
導入する機械は、包装機メーカーと生産する品目に合わせて会議などで仕様を決めていきました。機械が出来上がったときは、要求通りの仕様にできているかを確認するために、そのメーカーの工場に実際に機械を見に行きました。
そのとき、仕様通りに機械が製作され、問題なく機械が動いている様子を見てホッとしたのを覚えています。1年以上メーカーとやり取りをしながら、つくっていったものでしたから。
建物を建設する間、発電機を使った仮設電源で工事をします。小さな照明器具だけの、いわゆる工事現場という感じの環境で。
そこから建物が出来上がり、いよいよ送電直前の最終試験となりました。建設会社と立ち会い、全部の作業が完了したことを確認、そして送電。建物内の各所に明かりが点灯し、設備が動き出し、さまざまな音が鳴り響きました。工場に息が吹き込まれたようで感慨深かったですね。
いろいろな部署と折衝を繰り返して、2年が経過していましたから、ようやくここまで来たかという思いでした。ただ、登り切ったというイメージではなく、ようやく登り始める入口に立ったという気持ちでした。設備を使って製造が始まっていって、じわじわと達成感が沸いてきた感じですね。
プロジェクトでの経験を通じて成長を感じた点は?
新棟建設に携わる前は、設備が揃ったところで業務を行っていく立場でした。設備導入も初めての経験。機械を入れるために、どのような部署とどんな話をして、どんな資材が必要でどう段取りをしていくか、いろいろ学べたことは大きいですね。視座が少し高まったと感じています。
電子指図作成に携わる中で、「誰が・いつ作業をしても同じ品質の医薬品を製造できること」が、サワイの品質に繋がるということを改めて感じ、その大事さを再認識しました。
今はまだシステム担当で、実際に製造業務には携わっていませんが、製造に携わる者として意識が大きく変わったことを実感しています。
専門分野をより深く経験したのはもちろんですが、各部署と連携し、コミュニケーションを重ねた経験の中に学びがありました。
これまでのメンテナンス業務は、それぞれの領域が割と決められていて、その中で修理などの作業をしていました。1人で完結する仕事も多く、他の人と一緒に作業をすることも少なかったのです。
今回のプロジェクトは、各チーム、各部門との折衝など大変なことも多かったのですが、チームで戦うことの楽しさと難しさを学べたと思います。
また、部署ごとの要望に応えることは、部分最適であって最適解ではないかもしれない、「常に工場全体を見据えて、全体最適で解を導かなくてはいけない。」そんなことに気づくことができたのは、生産・製造に携わる者として大きかったですね。
※こちらの掲載情報は2025年3月末の情報です。